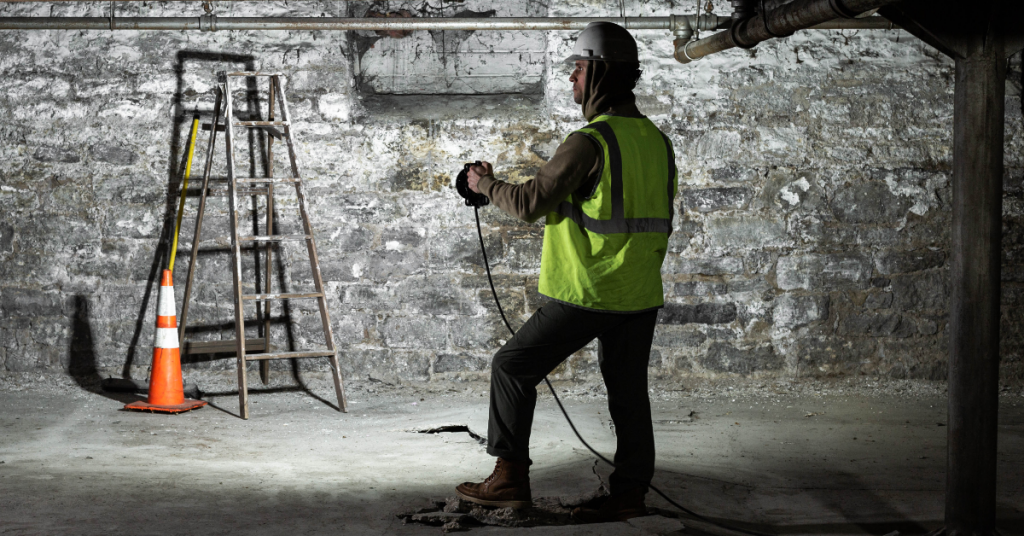
Shedding Light on Safety: Understanding Hazardous Location Lighting Regulations
Hazardous location lighting is designed to be explosion proof and to contain any sparks or fire that may occur inside the device. Hazardous locations can present unique and high-risk challenges that make finding the proper explosion proof lighting critical. With a commitment to safety and compliance, the KH Industries HazRay line of portable LED hazardous location lighting can be the ideal solution for your application.
Understanding hazardous location lighting regulations can be overwhelming, but ensuring the proper safety of your employees and customers requires commitment to the guiding safety principles and industry standards. With many manufacturers presenting a “regulation” product but only meeting partial regulations and guidelines, it’s wise to do the homework necessary to ensure compliance when purchasing hazardous location lighting. Consulting with technical sales and engineering teams at KH Industries can help educate customers on the proper lighting solution for their unique application.
Understanding Hazardous Location Lighting Regulations
Before lighting products are considered, what determines a “hazardous location” for the purposes of electric equipment? There are a number of agencies that play a role in creating standards that affect lighting fixtures. The National Fire Protection Association (NFPA) – focused on fire, electrical and related hazards, the National Electric Code (NEC) – classifies risk levels for hazardous location lighting and the Department of Labor’s Occupational Safety and Health Administration (OSHA) – which enforces regulations to protect safe and healthy workplaces.
Defining what a hazardous location begins with the OSHA’s classifications as found in the Occupational Safety & Health Standards 1010.307(a)(1). The standard sets forth workplace safety standards, and indicates locations are classified “depending on the properties of the flammable vapors, liquids or gases, or combustible dusts or fibers that may be present therein and the likelihood that a flammable or combustible concentration or quantity is present.” Basically anywhere these things creates a risk of fire or explosion.
The standard goes on to note that each room, section or area needs to be considered individually to determine its classification. Some examples of hazardous locations are oil refineries, paint booths, food processing plants, textile dyeing and printing plants, aircraft hangars, gasoline dispensing and service stations, bulk storage plants for gasoline or other volatile flammable liquids, paint-finishing process plants, health care facilities, agricultural or other facilities where excessive combustible dusts may be present (ex. Grain silos), marinas, boat yards, petroleum and chemical processing plants and cannabis processing plants. Each location has the potential to contain a risk of fire, explosion, property damage, environmental harm and harm to human life.
C1D1 vs. C1D2 – What’s the Difference?
The NEC classifies hazardous locations in articles 500-516 by definition. Class I locations are the strictest and are defined as those locations in which inflammable gases or vapors are or may be present in sufficient quantities to produce explosive or flammable mixtures. Class II locations are those that are hazardous because of the presence of combustible dust. When looking for proper explosion proof lighting, check out the KH Industries HazRay, a line of lighting that meets the stringent Class I & II classification requirements you may need on your job.
Class I, Division 1, or CID1, is a classification that describes a hazardous location where fire hazards (flammable gases or vapors) may be present during normal operations in sufficient quantities to create an explosive or ignitable situation under normal operation. Risk may be present continuously, intermittently, periodically or during normal operations, or where fire hazards exist and may or will lead to an explosion due to the regular presence of flammable materials. C1D1 environments specifically include hazardous materials that can catch fire and lead to explosions on a regular basis. This means that all electrical equipment must be designed to prevent sparking or internally contain an adverse reaction if one were to occur. This includes explosion proof enclosures, seals and other protective measures.
Class I, Division 2, or CID2, is a classification that describes a location that is defined by regularly using volatile hazardous materials that are prone to fire risk, but are explicitly kept in sealed containers or within closed systems. In these locations, the flammable or explosive materials are only in the open in the case of accidents, breakdowns, leaks, deterioration of the containers or systems that lead to the release of flammable substances. Electrical equipment in CID2 locations must be designed to prevent the ignition of flammable gases or vapors under normal conditions and designed to minimize the risk of ignition under abnormal conditions.
Class II, Division 1, or C2D1, includes locations where combustible dust may be in suspension in the air and can produce explosive mixtures under normal conditions or when conditions exist that can provide an ignition source where there is also a failure in equipment.
Class II, Division 2, or C2D2, is a classification that describes locations where combustible dust is not normally in suspension during regular operations, but where accumulation of dust can interfere with electrical equipment or ignite electrical equipment.
Each classification can also be broken down into specific zones that are further defined in the regulations. Be sure to check the specifications related to your worksite location when choosing the proper hazardous location lighting. The KH HazRay comes in a single handheld light, a stringer light and a multi-head option. Please review the specs for each model to ensure it is compliant with your requirements.
IP & T Ratings
Another thing to consider with hazardous location lighting is the Ingress Protection (IP) rating of the light. IP testing is a standard for classifying the degree of protection provided against dust, water, accidental contact and the intrusion of solid objects. The IP code on hazardous location lighting is what determines how protective it is against these elements. The IP ratings are assigned to equipment in the form of two-digit codes (ex. IP66 – like the KH HazRay). The first digit in the IP code is the level of protection to solid objects on a scale from 0 to 6. The second digit in the IP code indicates the level of protection against water and other liquids. This is on a scale from 0 to 9.
Most hazardous location luminaires must have an IP rating of at least IP54, and the higher the number, the more protection it provides. The KH HazRay is rated IP66 which means the light is protected from total dust ingress and high pressure water jets from any direction. This rating also encompasses all the lesser protections such as condensation, water spray from any direction and low pressure water jets.
The NEC also requires that all heat-producing equipment used in hazardous locations indicate its operating temperature by a T-rating number. It measures the hottest area in or on the equipment. The class, from 1 to 6 indicates the highest temperature allowed without igniting anything in the area. A lighting fixture is only considered thermally suitable for hazardous locations if the T-rating is lower than the ignition temperature. This is why most hazardous location lights operate at a lower temperature than most standard lighting fixtures, as not to be the source of an explosion. While some permanent explosion proof lighting is rated T6, most of the portable hazardous location is rated at T5 (100°C) like the KH HazRay.
Importance of Compliance
Why is it so important to comply with the Class I & II lighting requirements? In a nutshell, the reasons are safety related, financial, legal and reputation. Safety being the most important.
Compliance with Class I & II lighting requirements is crucial for ensuring the safety of workers and the integrity of operations in hazardous locations. Hazardous locations have an increased risk of fires, explosions and catastrophic incidents. There are so many industries and jobsites that require utilizing lighting equipment within an area that could potentially become dangerous. Too often, enough research has not been completed and employees are working with lighting equipment that does not meet the Class I & II requirements. Additionally, there are many lighting manufacturers out there that take shortcuts, outsource product, or overtly misrepresent their products, leaving companies thinking they are providing safe equipment when they are not. Hazardous location lighting is extremely important in ensuring the overall well-being of a business, and most importantly its workers.
The threat to worker safety can also result in legal and regulatory penalties, fines and sanctions. OSHA has established industry standards and codes to regulate hazardous locations and noncompliance with these standards and codes can result in harsh penalties and fines amounting to $15,000 per violation. Additionally, businesses found using non-compliant lights in hazardous locations may potentially be subject to severe legal prosecutions. Businesses may also find themselves dealing with financial losses due to downtime, litigation, insurance claims, and compensation payouts.
Non-compliance with standards can result in fines and legal action, but there are additional ramifications. If the wrong hazardous location lights are used or do not comply with the appropriate standards, they will have to be replaced with ones that meet the OSHA, NFPA, or NEC codes. In the end, there can be considerable long-term cost savings and risk mitigation through the use of compliant portable lighting solutions.
Challenging hazardous environments call for durable lighting that meets critical standards. The wear and tear on “lesser” non-compliant lighting options in these extreme environments can cause product failure due to lessened durability. This is another case for having to replace lighting at considerable expense to ensure it can provide enough light for the job and stand up to the hazardous location environment they are installed in.
Additionally, non-compliance to the standards can also damage the reputation and credibility to the business. Trustworthiness from both employees and customers is critical for a long standing place in the industry and companies that prioritize safety and compliance will be known for that.
Watch for Pitfalls & Deceptive Practices in the Industry
When researching temporary explosion proof lighting options, it’s important to make sure that the options being considered truly meet industry standards and guidelines. The lack of transparency or negligence to quality lighting can be seen online and with products made both domestically as well as offshore. The increased risk of fire and explosion from non-compliant products is real and the protection of workers and assets in hazardous environments should be paramount. This is why it’s important to fully research the portable explosion proof lighting options before a business finds themselves with legal and financial implications for using non-compliant lighting.
Frequently found are examples of manufacturers misrepresenting product certifications, or presenting claims of product certification that are actually only partially certified. An example of this is a certified CID1 light but with a non-certified plug attached. Or a certified luminaire with a non-hazardous location plug or mounting accessory. Another example is when a manufacturer will present the entire solution as certified, when only part of the solution meets industry standards. Or each of the parts meet it on their own, but not when compiled together. It is critical that the solution should be tested and certified in its final form.
The HazRay Difference: Compliance and Quality
The KH HazRay line of portable hazardous location lighting options provides the ideal solutions for a variety of environments and applications. Available in a single handheld light, a stringer and a multi-head light that can take from 1-5 lamp heads, these 120 volt lights can be configured in a variety of ways to suit many needs. The LED wide angle beam angle is 120°, providing wide area illumination in a low profile light, great for tight spaces. The body of the HazRay is constructed of durable, impact-modified ESD engineered thermoplastic and the LED module is constructed with shatter resistant glass making this light perfect for extreme environments. NEMA 4X and IP66 rated, these lights are suitable for web locations.
Certified in the US and Canada, the HazRay comes in 3 model types and specifically outlines the approved areas so customers are able to make decisions on what they need with full transparency.
The HazRay Single and Stringer are approved for use in the following areas:
- Class I, Div 1, Group C&D
- Class I, Div 2, Groups A-D, T5 (100°C), Class II, Groups E, F & G
- Class III
- Zine 1 IIB
- Certified to UL 844
- Certified to CSA C22.2 No. 137
The HazRay Multi-Head luminaire is approved for use in the following areas.
- Class I, Div 1, Group C&D
- Class I, Div 2, Groups A-D, T5 (100°C), Zone 1 IIB
- Certified to UL 844
- Certified to CSA C22.2 No. 137
Conclusion
In conclusion, the focus on portable explosion proof lighting should be centered on safety, compliance and meeting industry regulations to ensure safety for employees and customers alike. When looking for the ideal hazardous location lighting solution, choose a manufacturer with a quality assurance process to ensure compliance throughout manufacturing as well as transparency in certification and compliance documentation. Even after installation of the hazardous location lighting fixtures, compliance will need to be maintained regularly as operating conditions, practices, and equipment change.
Contact us for your portable hazardous location lighting needs and learn more about their commitment to providing compliant solutions with the HazRay line. In addition to the three standard models listed above, KH is fully staffed with technical sales and engineering departments that are capable of providing unique, custom solutions for every application. Contact us today!
0 Comments